This factory is different in other ways, too. “We do not weld; we have no rivets, no screws and no bolts. We just glue components together,” says Ulrich Kranz, the head of the division that since 2013 has been making BMW’s i3 and i8 electric and hybrid vehicles in Leipzig. Since the carbon-fibre body provides the vehicle with its strength, the outer panels are mainly decorative and made from plastic. These are simple to spray in a small paint booth, whereas metal requires elaborate anti-corrosion treatment in a giant and costly paint shop. In all, the i3 factory uses 50% less energy and 70% less water than a conventional facility.
The i-series are upmarket cars, but still produced in volume. BMW has succeeded in taking a new material hitherto used in low-volume specialist applications, such as aerospace and defence, and turning it into something close to mass-produced. That called for radical changes. When in 2007 the BMW board asked Mr Kranz to come up with an electric city car and a low-energy production system, he and his team went into hiding to allow ideas to flow freely.
Mr Kranz’s material of choice was carbon fibre, not least to offset the weight of the battery. The material is made from thin filaments of carbon woven into a cloth. This is cut and pressed into the shape of a part and the fibres bound together with a plastic resin, cured by heat and pressure. The molecular structure of carbon compounds produces strong chemical bonds, much like those in diamonds, and by aligning the fibres at different angles the strength of a component can be reinforced exactly where needed.
The resulting structure, although stronger than steel, is at least 50% lighter, and also about 30% lighter than aluminium. Nor does it corrode. But in the past the production process was expensive, slow and labour-intensive. That may not matter too much when making fighter jets or Formula 1 racing cars. But even aircraft-makers had to speed things up and bring down costs when they started making passenger jets from carbon fibre.
Look, few handsThese days carbon fibre makes up about half the weight of aircraft such as the Boeing 787 Dreamliner or the Airbus A380 and A350. Lighter aircraft burn less fuel and thus have lower emissions. They can also carry more passengers and fly farther. There are economies in manufacturing, too, because large sections of the aircraft can be made in one go instead of having to join together lots of smaller aluminium panels. Aircraft-makers have found ways to speed up some of the production process, but it is still too slow and expensive for high-volume carmakers.
The answer that BMW came up was a different sort of factory and a new supply chain. It begins in Otake, Japan, with a joint venture between SGL group, another German company, and Mitsubishi Rayon. This produces what is called a precursor, a polyacrylonitrile thermoplastic, which looks a bit like fishing line wound onto large spools. This is shipped across the Pacific to Moses Lake in Washington state, the site of another joint venture, this one between BMW and SGL. The location was chosen because it uses locally generated emission-free hydroelectric power.
Black carpetThe precursor is passed through a series of heating stages in which it is carbonised into blackened filaments only around 7 micrometres (millionths of a metre) in diameter. Some 50,000 of these filaments are bundled together into a thicker strand and wound onto reels, much like a yarn in a textile factory. The tows, as the carbonised yarns are called, then cross the Atlantic to another BMW-SGL joint venture, at Wackersdorf near Munich. Here they are woven into sheets and layered into stacks that resemble carpets.
When the stacks arrive at the Leipzig factory, they are heated and pressed into a three-dimensional “preform”. Various preforms are placed together to make up large structures, which together are pressed again, but this time resin is injected into the mould, bonding and curing the final component inside the press tool. This usually happens within minutes, though in some aerospace factories the curing can take the best part of a day and requires a pressurised oven called an autoclave. Robots move the parts around and glue them together to make the main body structure of the car. Further along the production line the body is mated to the drive module, which incorporates an aluminium chassis, electric motor, battery and other components.
Mr Kranz expects carbon fibre to be used more widely in cars, but thinks they will always contain a mix of materials. BMW’s new 7 series executive car now has some carbon-fibre parts as well. Other carmakers are starting to use the material, and Apple, which has hinted that it plans to build an electric car, has reportedly been talking to BMW about carbon-fibre construction. Anthony Vicari, an analyst with Lux Research, a Boston consultancy, predicts that by the mid-2020s carbon fibre will be widely adopted in carmaking.

But not without a battle. As in other industries, traditional materials are getting better, too. Aluminium suppliers are developing new alloys. “Aluminium is the incumbent and these guys are pushing like hell or they will lose their entire industry,” notes Jean Botti, the chief technical officer of Airbus. Alcoa, a leading producer of aluminium, is developing a number of lightweight alloys. One of them, Micromill, is easier and faster to shape into intricate forms. Ford has begun using it to replace some steel components in its F-150 pickups, one of its best-selling models in America.
The upshot is that manufacturers are being offered a wider choice of materials than they had before, says Mr Botti. Carbon fibre has done wonders in aerospace, he reckons, but it is used largely in the bigger, long-range aircraft, of which only a handful might be built every month. To increase the use of carbon fibre in smaller aircraft, aerospace firms have to speed up production and bring down costs further, but “there are new techniques we are thinking about which could tremendously reduce the cost of carbon fibre.” Airbus and Boeing both have plans to raise production of their workhorse short-haul aircraft, respectively the A320s and 737s, to an astonishing 60 or so a month to meet order backlogs. Still, he cautions, companies should always take care to select the best material for a particular job. If Airbus were to replace the A320 with a new model, he says, he would have to look carefully to see if carbon fibre provided the best value in a short-haul aircraft.
Airbus is also developing its own new materials. One of these is a proprietary aluminium-magnesium-scandium alloy called Scalmalloy. It is particularly good for making lightweight high-strength components. It is being commercialised by an Airbus subsidiary and is already used in some racing cars. In powder form, Scalmalloy can also be employed in a revolutionary form of manufacturing that is ideally suited to working with many new materials: additive manufacturing, popularly known as 3D printing
3D printing: Print me a pavilionAdditive manufacturing is a perfect way of using new materialsCARMAKERS can spend a year building a working prototype for a new car. Setting up machines for a production run of one is laborious and costly, since much of the work is done by hand. But researchers in Tennessee have an automated system endearingly known as BAAM (Big Area Additive Manufacturing). Most people would call it a 3D printer, albeit a particularly large one—and it is used to print cars.
The researchers work at the Oak Ridge National Laboratory, which is exploring a number of advanced manufacturing methods. BAAM was cobbled together from various bits of factory kit in partnership with Cincinnati Inc, a machine-tool company. In one experiment it made most of the body and chassis for an electric replica of a Shelby Cobra, a classic 1960s sports car. The printed parts that went into the vehicle were built up using a mixture of 80% polymer and 20% carbon fibre and weighed a mere 227kg. It took the team just six weeks to design, print and assemble the car.
A few companies, such as Local Motors, a firm based in Phoenix, are using additive technologies to make limited runs of cars, but 3D printing is still too slow for mass-produced vehicles. Even so, it will quickly become part of the automobile industry, says Thom Mason, director of Oak Ridge, not just for prototyping or customising vehicles but also for making moulds, tools and dies. That business had been largely offshored to low-wage countries. “Now we can print these things overnight,” explains Mr Mason.
Making things with 3D printers has captured the public imagination. In recent years, improved hardware and software has turned the basic technology—which is about 20 years old—into a broad assortment of different processes. They all rely on building up layers of material additively, using plastics, metals, ceramics and even biological feedstocks. Such printers range from desktop machines that cost a few thousand dollars to hulking monsters to print metal parts that cost over $1m.
The size of what could be printed used to depend on what would fit inside the machine. Now some printers, such as BAAM, are coming out of the box, so to speak. MX3D, a Dutch startup, plans to print a 15-metre (49-foot) footbridge across a canal, using robots fitted with steel-printing equipment. Winsun, a Chinese firm, uses a fast-drying mixture of cement and recycled construction waste to print prefabricated sections of buildings, and Achim Menges at the University of Stuttgart is printing strands of carbon fibre to make one-off architectural structures such as pavilions (pictured).
Strand by strand
One of a kindOne advantage of producing something additively is that material is deposited only where needed, so there is little waste. In traditional manufacturing perhaps 80% of the material is cut away. Moreover, the software used to design a product can also run the printer. And software is easy to tweak, so a different design can be produced every time without having to reset machines. The technique also lends itself to making complex shapes in new materials that can lead to dramatic performance gains. And although 3D printing is still slow compared with mass-production processes such as pressing steel and plastic injection moulding, in some industries that may not matter too much.
“Additive techniques give you a whole new degree of freedom,” says Mr Idelchik at GE Research. The company has spent $50m installing a 3D printing facility at a plant in Auburn, Alabama, to produce fuel nozzles for the new LEAP jet engine it is making in partnership with Snecma, a French company. GE will begin by printing 1,000 nozzles a year, but eventually the number could reach 40,000. The fuel nozzle in a jet engine is a complex part that has to withstand high temperature and pressure. Normally it is made from 20 different components. GE instead prints the part in one go, with a laser fusing together layers of a powdered “super alloy” made up of cobalt, chrome and molybdenum. The resulting nozzle is 25% lighter and five times more durable than the old sort, and conventional manufacturing methods might not have been able to cope with the material at all.
“Additive manufacturing will definitely win a lot of ground at the expense of existing processes,” says Henrik Runnemalm, the head of engines for GKN Aerospace, a British company. Some of GKN’s 3D-printed components are already in aircraft and jet engines. The technology is also used alongside traditional techniques. Mr Runnemalm cites an example in which a fine wire of material is melted to build up shapes on a component that has been cast in a conventional manner. In yet another process, a 3D printer creates a component in its “near-net shape” (close to its final form), which is then finished conventionally with machine tools.
Additive manufacturing has plenty of potential left, not least because it can change the properties of materials as it goes along. At Oak Ridge, researchers are working on specifying the crystalline structure of a metal in different parts of a component by fine-tuning the heat as the layers are built up, hoping to obtain different performance characteristics. “This is totally new,” says Mr Mason. “It is one of those things that is not in our design vocabulary right now.”
3D printing is capable of even more. Modumetal’s nanolaminates are also produced by additive manufacturing. The process takes place close to room temperature, which means metal could be added to a 3D-printed plastic shape, creating hybrid plastic-metal composites, says Ms Lomasney. And the process could run in reverse, dissolving the metal in a component back into a solution so that it could be used again. “We haven’t got into the business of recycling because parts are not yet being returned to us,” explains Ms Lomasney, “but in theory it’s possible.” With many new materials, recycling may become an essential requirement.
What next: Bright angelic millsThough recycling will become more complicated, a much wider choice of materials will transform manufacturingMANUFACTURERS are coming under growing pressure to take responsibility for the life cycle of their products. This involves an obligation to consider all the energy, environmental and health effects of every stage, from materials extraction to production, distribution and, eventually, recycling or disposal. As materials become more complex, that is becoming trickier.
The traditional way of gauging what effects a new material will have on the wider world is to go by the elements. If something has lead in it, for instance, it is probably not good for you. If it has a bit of manganese, it is probably safe. “That is so old-fashioned,” says Berkeley’s Mr Ceder. “Very often what these things do to your body depends on the form, not the chemistry.”
That makes nanoparticles particularly difficult. A lot of research is being done on their environmental and health implications, but much of it is inconclusive. A big five-year study of nanoparticles led by the Swiss National Science Foundation is due to be published in 2016. One example of its work, from Australia, illustrates the concerns.
Being a highly developed region, South Australia gets plenty of nanoparticles in products, some of which are washed into the drainage system. It is a dry place, so much of the wastewater is recycled, and treated sewage is used to fertilise fields. That allowed researchers from the Swiss Federal Laboratories for Materials Science and Technology to study the area as something of a closed system. From field and water deposits, they calculated the amounts of four nanomaterials that ended up in the environment every year: 54 tonnes of nano titanium dioxide (used in sunscreens); 10 tonnes of nano zinc oxide (found in cosmetics); 2.1 tonnes of carbon nanotubes (hollow tubes used instead of fibres in some composites); 180 kilograms of nano silver (for anti-bacterial use); and 120kg of fullerenes, another nano form of carbon, made up of hollow spheres known as “buckyballs”.
The final destination of these particles varied. The nano carbons remained embedded in the parts they came in, which ended up in rubbish dumps. The zinc oxide and silver were chemically converted into normal compounds in sewage-treatment plants, so did not seem to present a risk. But the nano titanium dioxide from sunscreens went walkabout. Just over 5% ended up in the sea, the rest on fields. In its normal form titanium dioxide is not toxic (it is used in toothpaste as well as sunscreen), but the researchers say they do not know what the long-term effects of the nano versions will be, especially in high concentrations.
Going dottyCertain nanoparticles undoubtedly have nasty effects. Some LEDS use quantum dots—tiny crystals which when excited by an external light source glow brightly, a process called luminescence. This produces richer lighting and brighter colours in LED televisions and other displays. The dots, though, are often made from a toxic cadmium compound. That provides a commercial incentive to come up with safer materials.
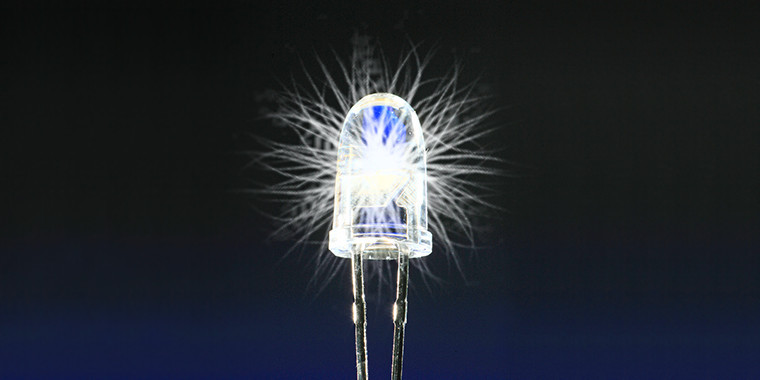
Loking for the perfect LED
Nanoco, a firm based in Manchester, has developed cadmium-free quantum dots. The Dow Chemical Company has licensed the technology to make dots at a new factory in South Korea. And Prashant Sarswat and Michael Free of the University of Utah have made quantum dots out of carbon obtained from food waste. This is put into a solvent and heated under high pressure. The process still needs to be scaled up, but as the raw ingredients are free and relatively safe, the idea has promise.
For larger items, the end-of-life problems are just as challenging—and rather more visible. Both Airbus and Boeing have programmes for recycling their carbon-fibre aircraft. In that industry at least the numbers are limited to a few thousand, but if carmakers were to adopt carbon fibre on a larger scale, millions of old carbon-bodied cars would eventually have to be disposed of. In some cases the material can be shredded and used in lower-grade components.
Recycling exotic materials might become a necessity. Some elements are expensive and hard to find; they may come from only a handful of countries, such as China, which could restrict supply. Others, including some rare earths, are not found in large quantities and are hard to mine. Such substances are being increasingly used in electric and hybrid cars. As these become more widespread, new methods of dismantling and recovering materials will have to be found.
Marion Emmert and H.M. Dhammika Bandara at Worcester Polytechnic Institute in Massachusetts have developed a new and energy-efficient way to extract rare-earth elements from electric cars, in particular neodymium, dysprosium and praseodymium. They sliced up and shredded the motor and other drive components from an all-electric Chevrolet Spark and used a two-stage chemical-extraction method to separate the rare earths and other useful materials. The technology, they say, could be used for other products that contain motors and magnets, such as wind turbines and medical imaging equipment.
Some firms use a process called life-cycle assessment (LCA) to work out environmental impacts. “The idea is to evaluate, cradle to grave, a product or service,” says Christian Lastoskie, an expert in the field at the University of Michigan. LCA used to be carried out when a product had been on the market for a while and plenty of data were available. Now it can be done in advance with computer modelling. That means making and testing a number of assumptions about a new material or process, but the analysis can be a useful guide to possible environmental concerns and help a company with its selection of materials, Mr Lastoskie explains.
One project he has worked on, with backing from Sakti3, was a comparison of the life cycle of conventional lithium-ion batteries and solid-state ones. The results, published in 2014 in the Journal of Cleaner Production, suggested that even after allowing for uncertainties about the properties of the cells and the efficiency of the process used to make them, the use of solid batteries in electric vehicles would bring down energy consumption and reduce global warming.
All this points to the conclusion that manufacturing will become ever more complex and that the days of “me-too” factories, making similar products in much the same way, are numbered. Processes such as 3D printing make economies of scale irrelevant, allowing low-volume production and rapid customisation. As labour costs shrink in relation to total production costs, there is less pressure to move production to low-wage countries. That does not mean foreign companies will give up making things in China, but that more of the things they make there will be for the Chinese.
With computing costs falling all the time, being able to model the manufacturing process and the life cycle of a new material opens up markets to new entrants with new ideas. Only a decade ago it was widely thought that the world’s car industry would consolidate into less than half a dozen groups because the barriers to entry were so high. Now new carmakers are appearing everywhere; not just Tesla and, possibly, Apple, but also many small, specialist ones such as Local Motors.
Big companies, too, will increasingly compete by using exclusive recipes for new materials and customised production techniques. “If you just do a great design and use a manufacturing process which everyone else can use, you will run out of steam,” says Mr Idelchik at GE Research. “But if you have a proprietary manufacturing process which applies to proprietary materials, you are creating a long-lasting competitive differentiation.”
Trade secretsMr Idelchik is not alone in that view. BMW’s factory in Leipzig uses standard industrial equipment and robots. What makes it special is the company’s intimate knowledge of exactly how its materials are made and how to control the processes that turn them into cars. This goes to the heart of materials science. “We think we are pretty much ahead of our competitors because we have the complete process and material development in our hands,” says BMW’s Mr Kranz.
In future more firms will need to be on top of their materials. The days of trial and error are coming to an end as powerful research tools deliver scientific data of unprecedented depth. The tumbling cost of computer power makes that information available to companies of all sizes just as new production processes, such as 3D printing, transform the economics of manufacturing into something lighter and swifter.
Mastering the greater complexity of materials, as well as their design, engineering, production, supply-chain and life-cycle management, will require new skills and plenty of entrepreneurial talent. It may attract more people into an industry that is still trying to shake off an image of dark satanic mills. Manufacturing is entering a new age. Edison would have heartily approved.
Fonte:
The Economist